Blækprinteren har allerede givet os en fotoforretning og et bogtrykkeri på skrivebordet. Nu vil 3D-printeren også give os en fabrik i bryggerset.
Tidligere – for fem-ti år siden – krævede det et hold af værktøjsmagere og folk i blå kedeldragter at tage springet fra god idé til industriel produktion. Og der skulle fremstilles mange eksemplarer for at tjene millioninvesteringen i maskiner ind. I dag kan enhver blive sin egen producent og på få timer fremstille unikke genstande: Legetøj, mekaniske dele, smykker … Ting, der før krævede en fabrik, kan nu skabes på en 3D-printer. Selv biler kan printes.
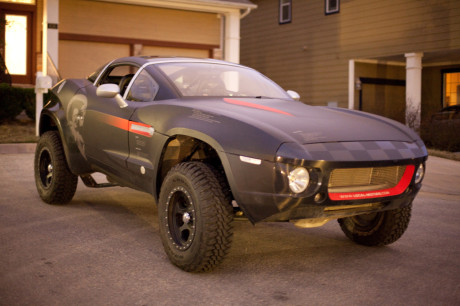
Og hvis du ikke har råd til at investere i en professionel 3D-printer, kan du få fremstillet dine opfindelser på 3D-trykkerier i ind- og udland. Et at de mest kendte er amerikanske Shapeways, der både fungerer som fremstillingscentral og salgskanal for 3D-print. Her kan man få virkeliggjort sine ideer i mangfoldige materialer, fra forskellige plasttyper over keramik og gummi til stål, sølv og guldbelagt bronze. Efter 10-15 dage ankommer tingene med posten.
“I gamle dage kunne man ikke som privatperson ringe til en fabrik og bede dem om at fremstille ting for sig. I dag har virksomhederne websites, og de er parat til at tage imod ordrer fra enkelpersoner. Kreditkort eller PayPal? No problem! Det er næsten ligesom at handle på Amazon,” siger Chris Anderson, der tidligere var chefredaktør på teknologimagasinet Wired, men nu ejer sin egen robotfabrik.

En ny industriel revolution
3D-print har på et årti bevæget sig fra at være en kostbar hobby for de få til at være tilgængeligt for de fleste. Og i den professionelle verden er de printede objekter rykket fra prototypelaboratoriet og arkitektkontoret ud i selve produktionshallen. I stedet for at støbe plast- og metalgenstande kan det hele printes ud. Et eksempel fra vores egne spalter er Motorolas modulopbyggede smartphone Project Ara, hvor både plastdele og elektronik skal fremstilles med 3D-printteknik.
Fortalerne for 3D-print mener, at vi står ved begyndelsen til en ny industriel revolution. En revolution, hvor massefremstilling i få store virksomheder bliver afløst af små serier eller unika skabt i en underskov af mikrovirksomheder. Enhver kan blive producent, og i en globaliseret verden kan vi alle sammen blive hinandens kunder og underleverandører via internettet.
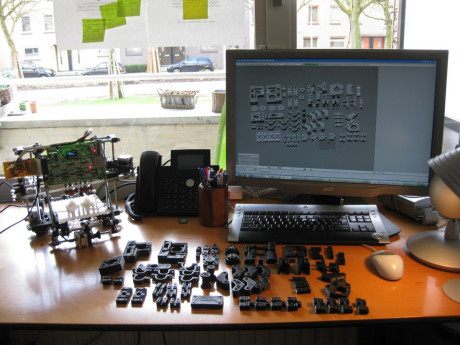
Din lokale bilfabrik
Da Henry Ford opfandt samlebåndet, revolutionerede det bilfremstillingen. Dengang var masseproduktion løsningen. I dag kan fem mand i en ombygget garage starte deres egen bilfabrik. Local Motors, som har fremstillet 3D-printede bildele siden 2010, har netop i slutningen af februar 2014 indgået en aftale om at udvikle den første 3D-printede elbil. Bilen skal være færdig til september.
Local Motors har i dag to såkaldte mikrofabrikker i henholdsvis Chandler, Arizona, og Las Vegas. Fabrikkerne er en kombination af fremstillingsvirksomhed, showroom og værksted. Og det er meningen, at kunder, der køber en bil hos Local Motors, selv er med til at bygge den i den nærmeste mikrofabrik.
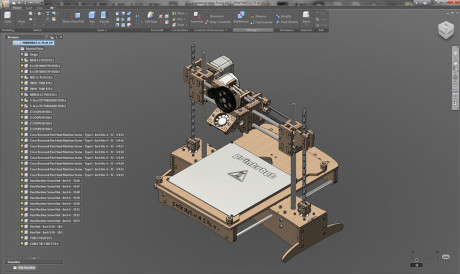
Det er Local Motors’ erklærede mål at starte 100 mikrofabrikker over hele kloden i løbet af de næste ti år. Så din næste bil bliver måske printet – lige henne om hjørnet og efter dine anvisninger.
Sådan bliver du din egen fabrikant
For at komme i gang skal du først og fremmest have en idé. Og den idé skal siden omformes til en 3D-model i en computer. Det er også en fordel at have (adgang til) en 3D-printer.
Tre faktorer betyder noget i 3D-printning: Udvalget af materialer, antallet af printhoveder og størrelsen. De fleste 3D-printere til hobbybrug printer ved hjælp af såkaldte filamenter, dvs. tråde, som oftest er i plastic. Hvis printeren er udstyret med ét hoved, kan man printe i et materiale ad gangen. Er der flere, kan mere komplekse objekter i flere farver eller materialer bygges op. Endelig bestemmer printerens fysiske størrelse, hvor store objekter der kan fremstilles.
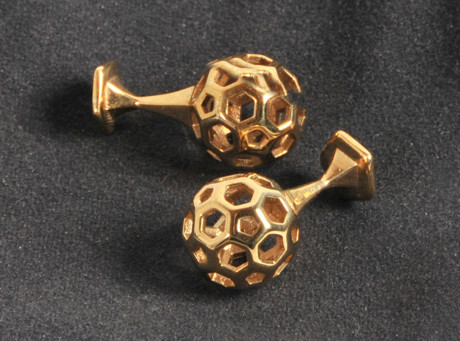
De første 3D-printere brugte gips som byggemateriale. De færdige figurer var forholdsvis skrøbelige, men blev modtaget med kyshånd af f.eks. arkitekter, som kunne bruge printeren til at skabe tredimensionelle modeller. Det mest almindelige materiale for 3D-print i dag er plast. En tynd plastictråd opvarmes i printhovedet, og der afsættes en klat på arbejdsbordet.
Hvad enten materialet er plast, kunstharpiks eller metal, kræves der en separat mekanisme for hvert materiale eller hver farve. De billigste modeller kan kun printe med ét materiale ad gangen. Det sætter en grænse for, hvor avanceret figuren kan blive. Er der brug for flere materialer eller flere farver, kan objektet dog printes i flere omgange og samles bagefter.
Ligesom man ikke kan udskrive en A2-plakat på en almindelig blækprinter, er arbejdsarealet på 3D-printere til hobbybrug begrænset. De fleste har et arbejdsområde på omkring 15 x 15 x 15 cm. Nok til at printe en plasticmodel af en bil, men ikke nok til at gå Local Motors i bedene.
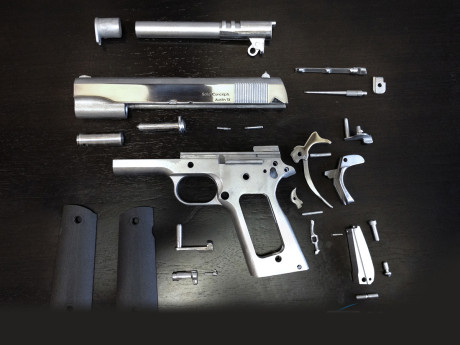
En printer der printer printere som printer printere
En gammel programmørvittighed lyder “rekursion: Se ‘rekursion’.” Da 3D-printere hidtil har været hjemmebane for teknologinørder og hobbyfolk, kræves der ofte en god portion håndelag og teknisk snilde for at komme i gang. Flere af byggesættene kræver således, at man selv printer plasticdelene til printeren. Det lader sig af gode grunde ikke gøre, men så må man låne af en ven. Derfor er det første, som en 3D-printerbygger sætter sin printer til at fremstille, i reglen en 3D-printer, så nye printerbyggere kan komme i gang.
Kan betale sig for de fleste
Ifølge skaberne af RepRap, som er den åbne standard bag mange hobby-3D-printere, vil den typiske familie have brug for at printe ti 3D-objekter om året. Ved at lave delene selv kan man typisk spare 200 til 2.000 dollars om året. Og det betyder, at de ca. 4.000 kroner, som de fleste billige 3D-printer koster, hurtigt er tjent ind. Og det tyder på, at priserne på 3D-printere kan blive endnu lavere. Vi skrev for nylig om den første 3D-printer, der koster under 2.000 kroner.
TRE 3D-TEKNOLOGIER
3D-printeren bygger tingene
I en 3D-printer bygges modellerne op på samme måde, som man udskriver et billede på en inkjet-printer: Én dråbe ad gangen. Dråberne er blot tredimensionelle og kan bestå af mange forskellige materialer. Alt, hvad der kan gøres flydende og derefter størkne, kan i princippet bruges til at opbygge 3D-figurer af. Foreløbig har vi set 3D-print af plastic, træ, ler, gips, sukker og forskellige metaller. Når der skal printes metal, bruges en laser til at smelte metalpulver.
CNC-fræseren – 3D-printerens fætter
Et alternativ til at printe er at opbygge figurerne med en computerstyret fræser. I stedet for at opbygge figuren af bittesmå klatter fræses den ud af en blok. CNC-fræsning gør det muligt at arbejde med endnu mindre detaljer end 3D-print, da der ikke skal tages højde for ujævn smeltning. Og man kan arbejde i materialer, der ikke lader sig smelte, f.eks. sten.
Fræsning har dog nogle begrænsninger med hensyn til, hvad der kan fremstilles, da værktøjet skal kunne komme til. Med 3D-print kan man f.eks. opbygge figurer, der befinder sig inden i hinanden. Det kan ikke lade sig gøre med en fræser.
Laserskæring
En helt tredje måde at fremstille 3D-modeller på er ved hjælp af laser. Teknikken er i familie med CNC-fræsning, men der skæres med en laserstråle. Her er der igen et særligt sæt muligheder og begrænsninger, men på plussiden tæller en meget høj detaljeringsgrad.
Læs også: Billig, stueren 3D-printer til skrivebordet